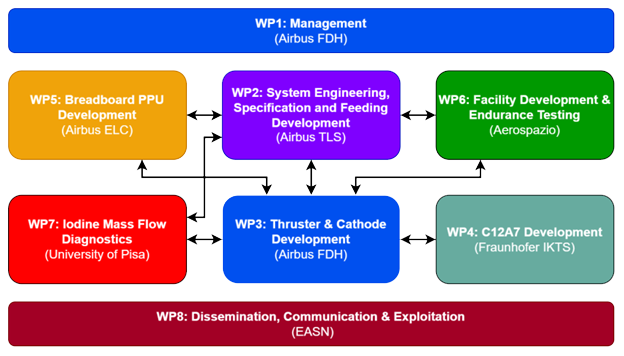
To ensure the successful implementation of iFACT-MP project, its effort has been divided into eight (8) work packages (WPs) as illustrated in the Work Plan above. It consists of six technical work packages (WP2-7) and two organizational work packages (WP1 and WP8).
Each WP will be led by the major executing entity of the included activity, with extensive experience on the specific topic, and each WP Leader will be responsible for the coordination with the consortium partners involved in their WP.
WP Leader: AIRBUS DEFENCE AND SPACE GMBH
The project management team is responsible for planning, organizing, coordinating, and controlling activities to achieve targeted goals. Their objectives include:
Effective Collaboration: Ensuring seamless coordination and collaboration among partners.
Goal Fulfilment: Overseeing the project to meet its overarching goals within specified time and budget constraints.
Quality and Timely Delivery: Assessing the quality and timely delivery of project results.
Cost and Effort Tracking: Maintaining accurate records of cost and effort reports from partners.
Risk Mitigation: Minimizing risks by developing contingency plans and implementing corrective actions as needed.
WP Leader: AIRBUS DEFENCE AND SPACE SAS
The primary objective is to adopt a comprehensive perspective that spans system engineering and platform considerations within the project framework. This involves conducting a meticulous market analysis, crafting a robust business plan, specifying the intricate details of the Electric Propulsion Subsystem (EPS) components, and closely monitoring the ongoing developments of our project partners. Furthermore, this work package goes beyond these essential aspects and encompasses a dedicated focus on advancing fluidics developments to enhance the overall functionality and efficiency of the project.
WP Leader: AIRBUS DEFENCE AND SPACE GMBH
Within the designated work package (WP), pivotal development activities center around advancing the Advanced Cusp Field Thruster (ACFT) and cathode components, extending to comprehensive subsystem-level activities. This multifaceted agenda encompasses several key elements:
Up-scaling of the ACFT: Implementing measures to enhance and scale up the capabilities of the Advanced Cusp Field Thruster, ensuring optimal performance within the designated power range.
Cathode Development: Engaging in innovative processes to refine and advance the development of the cathode, aiming for heightened performance and efficiency in the Electric Propulsion System.
Subsystem Integration and Coupling Testing: Rigorously testing the integration and coupling of subsystem elements to ensure seamless coordination and functionality within the broader framework.
Environmental Testing: Subjecting the system to thorough environmental testing, ensuring its resilience and performance under various conditions, aligning with the project's operational requirements.
Endurance Testing: Conducting extensive endurance testing to validate the sustained performance and durability of the system over prolonged operational periods, addressing the crucial aspect of long-term reliability.
This comprehensive approach within the work package underscores the commitment to advancing each component and subsystem, ensuring a robust and reliable Electric Propulsion System.
WP Leader: FRAUNHOFER GESELLSCHAFT ZURFORDERUNG DER ANGEWANDTENFORSCHUNG EV
WP4 aims to achieve several key objectives:
Provision of C12A7:e- Components: Delivering C12A7: e-ceramic components for effective electron emission.
Enhanced Electron Emission via Shaping Methods: Utilizing shaping methods to improve the surface structure of components, thereby optimizing electron emission efficiency.
Increased Melting Point for High-Temperature Performance: Elevating the melting point of components is targeted to ensure superior performance under high-temperature conditions.
Improved Compatibility with Iodine: Addressing material interaction challenges by enhancing the compatibility of electron-emitting C12A7:e- with iodine, ensuring seamless integration within the overall system (C12A7 refers to electron-emitting calcium aluminate compound material, specifically 12CaO 7Al2O3.).
WP Leader: AIRBUS DEFENCE AND SPACE SAS
The objectives for this specific work package (WP) are multifaceted and integral to the success of the overall project. The primary goals encompass the comprehensive definition, manufacturing, and debugging of a Breadboard Power Processing Unit (PPU). The PPU developed in this context is designed to serve a critical function - driving both the thruster subsystem and the fluidic regulation components.
Definition of PPU Breadboard: The work package involves a meticulous definition phase, where the specifications, functionalities, and requirements of the Power Processing Unit (PPU) breadboard are thoroughly outlined. This initial step is crucial for ensuring that the subsequent manufacturing and testing processes align precisely with the project's objectives.
Manufacturing of PPU Breadboard: With the defined parameters in place, the focus shifts to the manufacturing phase. Skilled professionals and cutting-edge technologies are employed to bring the PPU breadboard to fruition, adhering to the outlined specifications. This process demands precision and attention to detail to guarantee the reliability and functionality of the developed unit.
Debugging and Testing: Once manufactured, the PPU breadboard undergoes an exhaustive debugging phase. Rigorous testing procedures are implemented to identify and rectify any potential issues or malfunctions. This phase is critical in ensuring the optimal performance and reliability of the PPU, particularly in its role of driving both the thruster subsystem and the fluidic regulation components.
The comprehensive approach within this work package is geared towards achieving a high level of precision and reliability in the Breadboard Power Processing Unit. By successfully defining, manufacturing, and debugging this crucial component, the project aims to lay the groundwork for subsequent phases, contributing to the overall success of the Electric Propulsion System.
WP Leader: AEROSPAZIO TECNOLOGIE SRL
This work package (WP) is strategically aligned with consolidating and translating existing knowledge on iodine-fed Electric Propulsion (EP) system testing into a comprehensive test facility design. The primary objectives encompass the development of a test facility capable of safely and reliably operating with thrusters up to 5 kW. The specific goals within this WP include:
Update Safety Procedures: A critical aspect involves updating and enhancing safety procedures and measures to safeguard equipment, personnel, and the environment, specifically tailored to the power class of the thrusters in use. This ensures the secure and controlled operation of the test facility.
Design of the New Test Facility: A pivotal step is the design phase, where the new test facility is conceptualized. This includes incorporating features for thruster plume diagnostics and the implementation of a precise thrust measurement system. The design phase is meticulous and focused on accommodating the unique requirements of iodine-fed EPS testing.
Procurement and Assembly: Once the design is finalized, the next step involves the procurement and assembly of the test facility. This phase is critical for translating the theoretical design into a tangible, functional system. Attention to detail and adherence to design specifications are paramount during this stage.
Characterization of Iodine-Fed EPS: The final objective is to provide a comprehensive characterization of the iodine-fed Electric Propulsion System (EPS). This includes conducting a duration test lasting up to 500 hours, allowing for a thorough assessment of the system's performance, reliability, and endurance under sustained operational conditions.
The holistic approach within this work package is geared towards the establishment of a state-of-the-art test facility, ensuring safe, reliable, and controlled testing of iodine-fed EPS, up to 5 kW. Through systematic updates, design, procurement, and rigorous testing, the WP contributes significantly to the overall success and advancement of the Electric Propulsion System.
WP Leader: UNIVERSITA DI PISA
The primary goal of this work package is the development of a spectrophotometric Mass Flowmeter (MFM) prototype, advancing it to Technology Readiness Level 4 (TRL4). This prototype is specifically designed to integrate seamlessly with the iodine feeding system developed in WP2, with the capacity to measure instantaneous iodine mass flow during thruster characterization tests at rates up to 15 mg/s. The specific focus areas and activities within this WP include:
Design Prototype: The initial phase involves designing a modified version of the mass flowmeter originally developed by UniPi, tailored to the requirements of the iodine feeding system.
Manufacture MFM Prototype: Following the design phase, the prototype of the spectrophotometric MFM is manufactured with precision and attention to detail.
Characterize MFM Operation: Rigorous testing is conducted to characterize the operation and response of the Mass Flowmeter prototype in an environment that mirrors real-world conditions.
Integration with Feeding System: The MFM prototype is integrated seamlessly into the iodine feeding system developed in WP2, ensuring compatibility and efficient functioning.
Perform Coupling Test: Prior to the thruster experimental campaign, a coupling test is conducted to assess the integrated system's performance and identify any potential issues.
The successful implementation of WP7 significantly contributes to advancing the diagnostic capabilities of the iodine-fed Electric Propulsion System.
WP Leader: EASN TECHNOLOGY INNOVATION SERVICES BVBA
The primary objective of this work package is to formulate and implement a robust strategy for dissemination, communication, and exploitation. The key goals are outlined as follows:
Effective Strategy Elaboration: Develop and implement a comprehensive strategy for dissemination, communication, and exploitation, ensuring that project results reach a broad audience.
Wide-Scale Uptake: Facilitate the wide-scale adoption of project results by conducting targeted dissemination and communication activities tailored to each identified target group.
Awareness Creation: Generate awareness about the societal benefits derived from the project outcomes, with a specific focus on engaging and informing the general public.
Knowledge Protection and Open Access: Monitor and manage the protection of knowledge created within the project while simultaneously ensuring open access to the achieved results. Balancing protection with accessibility is a critical aspect of this goal.
Synergies with Other Projects: Develop synergies with other projects in related technological fields, fostering collaboration and information exchange to amplify the impact and reach of the project.
The overarching aim is to ensure the project's outcomes are effectively communicated, adopted, and appreciated across diverse target groups. This involves not only protecting intellectual property rights (IPR) but also fostering an environment of openness and collaboration within the broader technological landscape. Through strategic dissemination and communication, this WP plays a pivotal role in maximizing the societal impact of the project.